Is the future of other vehicles electric also?
- Marc Allen
- Aug 6, 2017
- 4 min read
In the last couple of posts, the focus has been on the drivers to electric vehicles - both commercial and policy drivers. For the most part though, these drivers are focussed on personal mobility and light vehicles. This does make sense as, according to the US EPA, light vehicle transport makes up the largest portion of transportation related emissions (in the US). But what about all of the other vehicles that are out there? What's happening with heavy duty road transport (e.g., trucks/road trains) and other equipment like mine site mobile equipment?
Currently, the technology for electrification of heavy vehicles has some way to go. The issue really is the battery density available in current battery technology. To generate the required output (i.e., range and duration of discharge), a lot of batteries are required, which then increases weight and reduces the amount of weight available for transport of commercial goods. There has been progress however. BMW recently started using a 40 ton truck on the roads in Munich which is completely electric. This truck has a range of approximately 100 km and a charge time of 3 - 4 hours. This is probably not enough to make it commercial yet, particularly for use in transporting goods between centres (like in Australia or the US for example). It is a start though and technology may improve over time. To make it viable however, a step change in battery chemistry technology may be required.
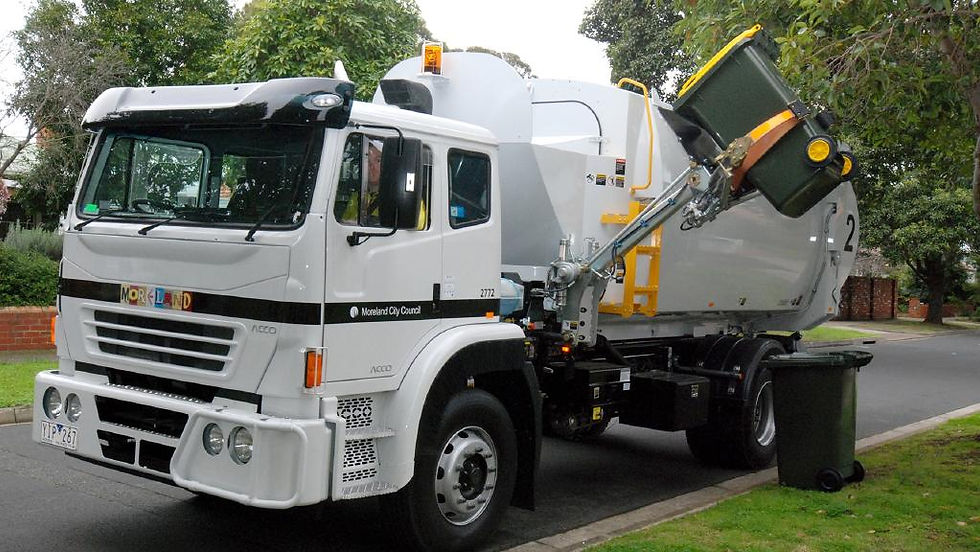
In the short term, the solution for emissions reductions in heavy vehicles will lie elsewhere. Fuel switching to lower carbon fuels such as compressed natural gas or liquefied natural gas is already happening. Diesel hybrid motors are also in use around the world. These will all act to reduce emissions from this sector. An interesting, and relatively new player is the use of hydrogen in heavy transport. In August 2017, there was an announcement from the Moreland Council in Melbourne that said they were building commercial hydrogen refuelling infrastructure and had plans to have 12 of their 18 garbage trucks as zero emissions vehicles by 2020. These will be hydrogen powered using hydrogen fuel cells. The refuelling station will generate hydrogen through onsite electrolysis using electricity supplied from a 1.2 MW solar power plant and imported electricity from a grid connected wind farm. Hydrogen has a number of advantages over batteries for heavier vehicles. The biggest of these being an improved energy density for storage of hydrogen on board and much shorter refuelling times - keeping the vehicles on the road for longer.
Electrification of mine site vehicles is likely to be something that sees increasing focus in coming years. Work has already begun from some manufacturers to electrify different types of mobile equipment. For example, Atlas Copco have released a battery powered underground bogger and Sandvik have released a battery powered development drill. In the case of the Sandvik product, it uses batteries and electric motors to get to the work area, then plugs into the normal power supply like a normal jumbo. The Atlas Copco bogger is completely battery powered. Battery powered underground and open pit haulage vehicles are still being developed. Like other heavy vehicles, current battery density is an issue. Having said that, there are examples globally that use electric trolley assist on large haulage vehicles. In these systems, the vehicles have traditional diesel power but main haul roads, particularly on inclines, have power lines overhead. The vehicles are also fitted with pantographs that extend up to the power lines and drive electric motors.
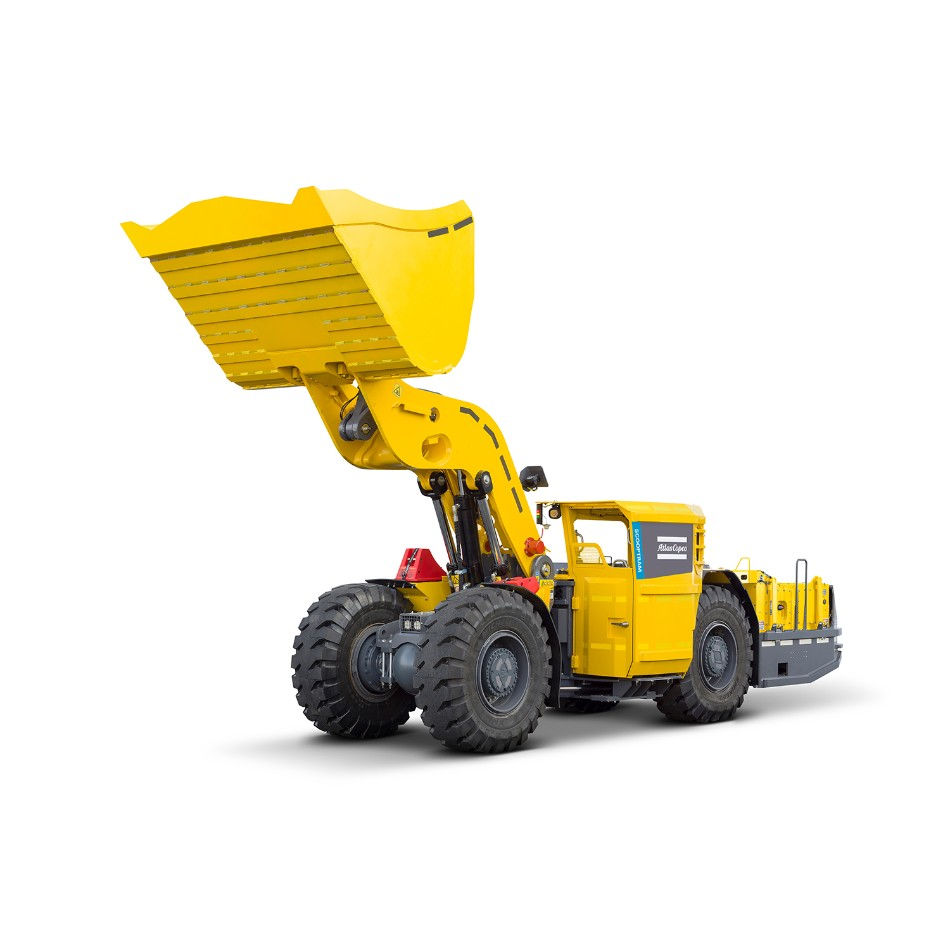
The use of battery powered equipment underground has a huge advantage in allowing for reduction in ventilation requirements. By and large, mine vent systems are designed around keeping diesel particulates at safe levels and a complex network of primary and secondary fans are used to maintain ventilation rates. Zero emissions equipment underground would mean that ventilation requirements could be reduced and additional power savings achieved. The main downside to using battery powered equipment in a mining context however is the time taken to recharge. To achieve good productivity from mine equipment, downtime should be minimised. Taking 3-4 hours to charge a battery on a piece of mining equipment will be seen as excessive. A potential solution might be to have a quick battery change out (i.e., a discharged battery pack with a charged one) to keep equipment operating for as high a proportion of the day as possible - though the additional capex of multiple battery packs for a single piece of equipment may also be prohibitive.
A site to watch will be the Borden Gold site, owned by Goldcorp and currently in development. They announced in November 2016 that this mine intends to use battery powered underground vehicles for almost all requirements. They have partnered with Sandvik and MacLean Engineering to develop battery powered drilling and blasting equipment, to electric bolters, personnel carriers and ultimately a 40 metric tonne battery powered haul truck.
In summary, it's still early days for the use of batteries in some of these heavy vehicle applications. There are many signs pointing to the fact that, unless there is a step change in battery chemistry and battery technology, another zero emissions fuel such as hydrogen may be more appropriate.